Bridging the Gap: Integrating Predictive Maintenance Alerts with Your Existing CMMS/EAM Systems
04/11/2025
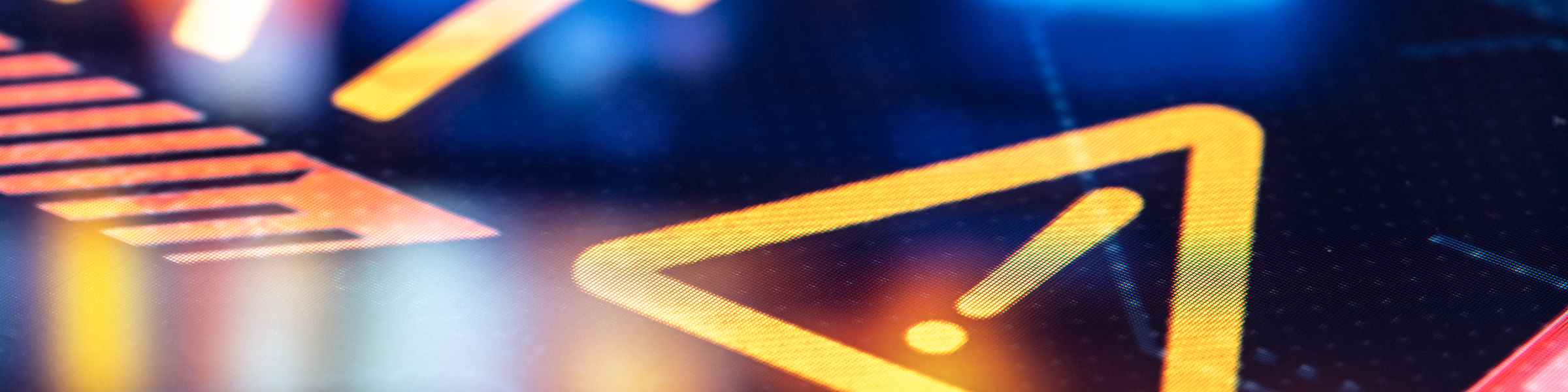
Predictive Maintenance (PdM) systems, powered by advanced sensors and AI, are transforming industrial maintenance by providing early warnings of potential equipment failures. These alerts are incredibly valuable, offering the potential to prevent costly downtime and optimize maintenance schedules. However, a common challenge engineers face is that these sophisticated PdM alerts often exist in a separate system, disconnected from the core maintenance workflow managed by Computerized Maintenance Management Systems (CMMS) or Enterprise Asset Management (EAM) systems. This data silo can hinder responsiveness and prevent you from realizing the full benefits of your PdM investment. At Blackhawk Equipment, we understand that seamless workflow is key. Let's explore why integrating PdM alerts with your CMMS/EAM is crucial and how to effectively bridge this gap.
Why Integration Isn't Just Nice-to-Have, It's Essential
Manually transferring information between a PdM platform and a CMMS/EAM is inefficient, prone to errors, and slows down response times. True integration unlocks significant operational advantages:
- Streamlined Maintenance Workflow: When a PdM system detects a potential issue, integration can automatically trigger a work order request or notification within the CMMS/EAM, complete with relevant diagnostic data (asset ID, alert severity, sensor readings, potential failure mode). This eliminates manual data entry and ensures the right information gets to the right people immediately.
- Faster Response Times: Automating the alert-to-action process significantly reduces the delay between detecting a potential failure and scheduling the necessary maintenance, minimizing the risk of the failure actually occurring.
- Improved Resource Allocation: Planners and schedulers using the CMMS/EAM have immediate visibility into predictive alerts alongside routine preventive maintenance tasks, allowing for better prioritization and allocation of technicians and spare parts.
- Enhanced Data Tracking and Analysis: Integration creates a closed loop. Maintenance actions performed are recorded in the CMMS/EAM, and this feedback (e.g., maintenance completed, parts used, actual condition found) can potentially be fed back to the PdM system to refine its predictive models. It also centralizes maintenance history for better long-term analysis.
- Reduced Manual Errors: Eliminating manual data transcription reduces the likelihood of typos or incomplete information entering the maintenance record.
- Maximized ROI: Integration ensures that the valuable insights generated by the PdM system are acted upon efficiently, maximizing the return on investment for both the PdM technology and the CMMS/EAM platform.
Understanding the Key Systems: PdM vs. CMMS/EAM
To integrate effectively, it helps to understand the core function of each system:
-
Predictive Maintenance (PdM) Systems:
Their primary role is to monitor equipment condition using sensors (vibration, temperature, flow, etc.), analyze the data (often using AI/ML), detect anomalies, and predict potential failures, generating alerts or recommendations. Examples include dedicated platforms analyzing data from sensors like those from VPInstruments or integrated capabilities within OEM equipment.
These are the operational backbone for maintenance management. They manage asset hierarchies, schedule preventive maintenance, generate and track work orders, manage spare parts inventory, record maintenance history, and provide reporting on maintenance activities and costs.
The goal of integration is to make these two distinct systems communicate and share relevant data automatically to create a cohesive maintenance ecosystem.
Common Challenges in PdM-CMMS/EAM Integration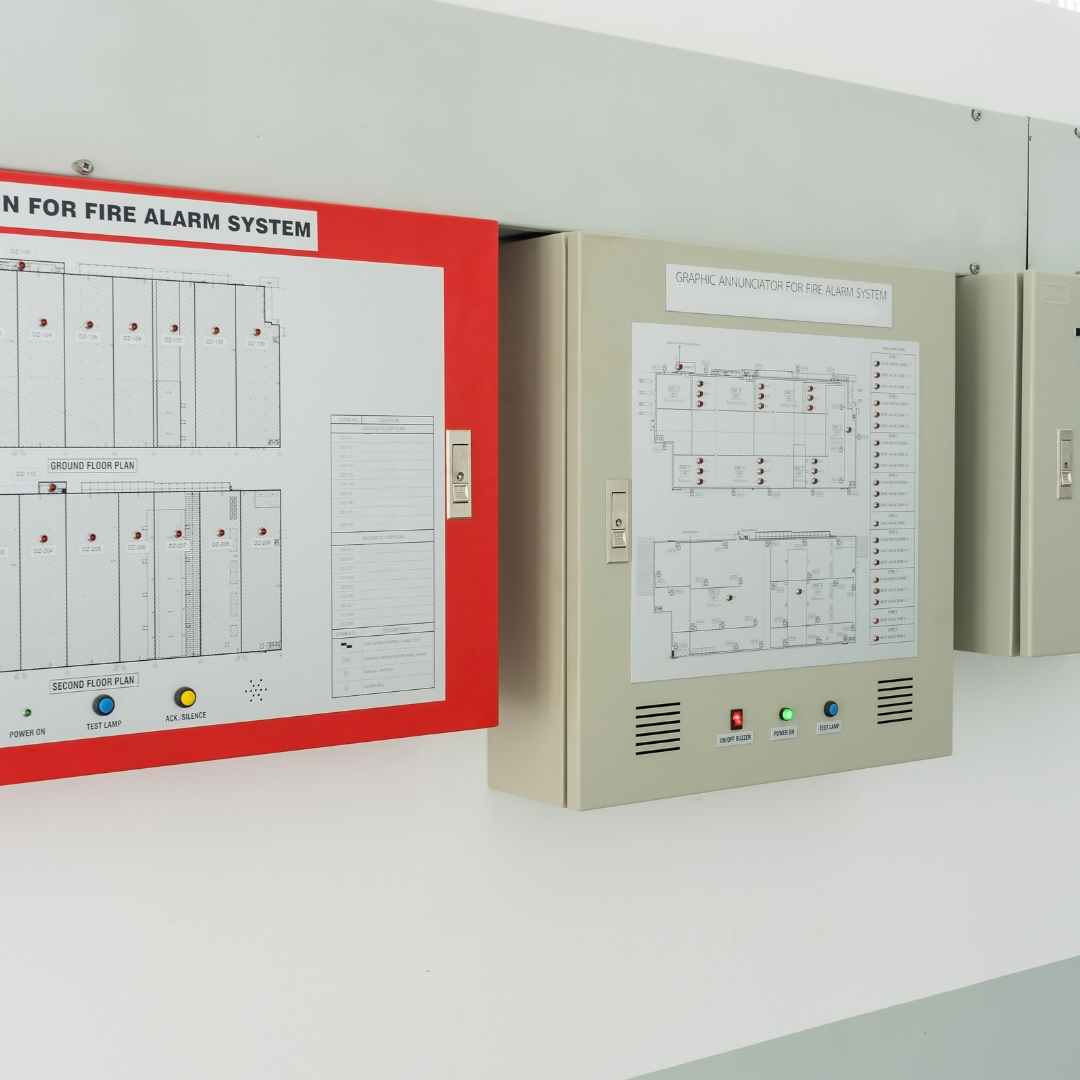
While the benefits are clear, integration projects can present hurdles:
- Technical Compatibility: Systems may use different data formats, communication protocols, or lack standardized APIs, making direct connection difficult.
- Lack of Standard APIs: While improving, not all PdM or CMMS/EAM vendors offer robust, well-documented APIs (Application Programming Interfaces) for seamless integration.
- Security Concerns: Transmitting potentially sensitive operational data between systems requires robust security measures to prevent unauthorized access or breaches.
- Legacy Systems: Integrating modern PdM platforms with older, less flexible CMMS/EAM systems can be particularly challenging.
- Data Mapping Complexity: Accurately mapping data fields between the two systems (e.g., ensuring Asset ID formats match) requires careful planning.
- Organizational Silos: Lack of collaboration between IT (often managing CMMS/EAM) and OT (Operations Technology, often managing PdM) can impede progress.
- Cost and Resources: Integration projects require investment in time, potentially specialized software (middleware), and skilled personnel.
Methods and Technologies for Successful Integration
Several approaches can be used to connect PdM and CMMS/EAM systems:
-
APIs (Application Programming Interfaces):
This is generally the preferred method. APIs act as standardized contracts that allow different software applications to communicate and exchange data securely and efficiently. Look for systems offering well-documented RESTful or SOAP APIs.
Integration Platform as a Service (iPaaS) or specialized middleware can act as a bridge between systems, handling data transformation, protocol conversion, and workflow orchestration. This can be useful when direct API integration isn't feasible.
-
Direct Database Connection:
While technically possible in some cases, directly connecting to the underlying database of either system is generally discouraged due to security risks, potential data corruption, and issues with vendor support or future upgrades.
Some systems might only support exporting alerts as files (e.g., CSV, XML) which can then be manually or automatically imported into the CMMS/EAM. This is the least efficient method and prone to delays and errors.
Key Steps for Planning Your Integration Project
A structured approach is crucial for successful integration:
- Define Clear Objectives & Scope: What specific workflow do you want to automate? (e.g., Automatically create a high-priority work order in CMMS when PdM issues a critical alert for Compressor X). Start small and focused if needed.
- Assess System Capabilities: Evaluate the integration capabilities (APIs, data export options) of both your PdM platform and your CMMS/EAM system. Consult vendor documentation and support.
- Plan Data Mapping: Carefully define which data fields need to flow between systems and how they correspond (e.g., PdM 'Equipment ID' maps to CMMS 'Asset Tag').
- Choose Integration Method: Based on system capabilities and objectives, select the most appropriate integration technology (API, middleware, etc.).
- Develop/Configure Integration: Implement the chosen method, involving IT, OT, and potentially third-party integration specialists.
- Implement Robust Security: Ensure secure authentication, authorization, and data encryption throughout the integration process.
- Test Rigorously: Conduct thorough end-to-end testing to validate data flow, trigger accuracy, and workflow execution. Involve maintenance end-users in testing.
- Train Users: Ensure maintenance planners, schedulers, and technicians understand the new integrated workflow and how to interact with the information.
- Monitor and Refine: Continuously monitor the integration's performance and make adjustments as needed based on user feedback and operational results.
How Blackhawk Equipment Can Support Your Integration Efforts
While Blackhawk Equipment may not directly perform complex IT integrations, we play a vital role. When we help you implement monitoring solutions like those from VPInstruments or deploy PdM strategies for equipment we supply or service, we prioritize solutions known for their data accessibility and integration potential. We can:
- Advise on selecting PdM hardware and software with strong API support or integration capabilities.
- Ensure data from monitored equipment is structured and accessible for integration purposes.
- Collaborate with your IT/OT teams or third-party integrators to provide necessary information about the monitored equipment and data streams.
- Help you understand the meaning behind the PdM alerts generated from the utility systems we know best.