Cameron Compression Systems: Powering Critical Operations with Engineered Reliability
02/28/2025
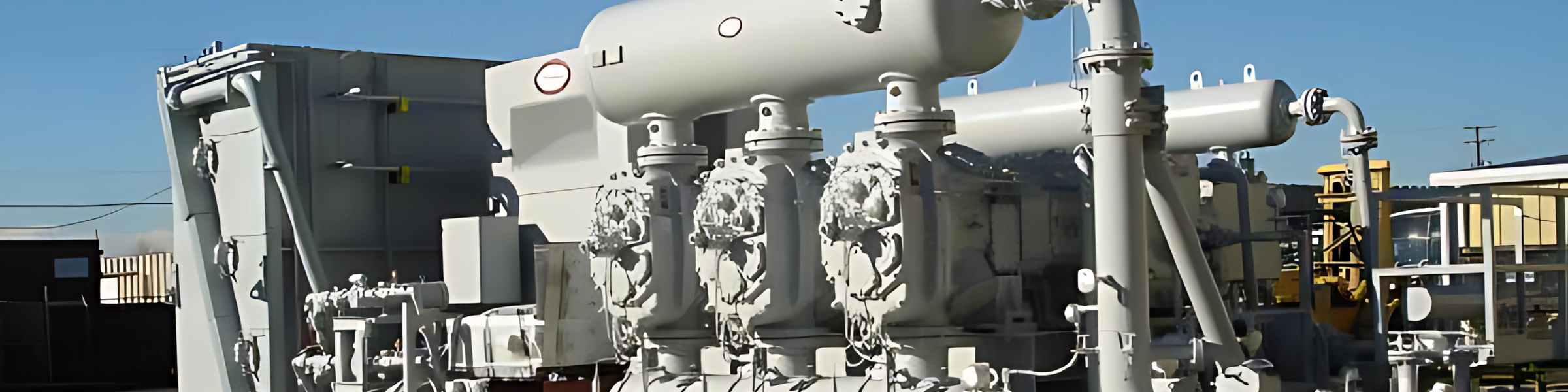
In industries where downtime is not an option and performance is paramount, Cameron compression systems have earned a reputation for engineered reliability. Now a part of Schlumberger, Cameron brings a legacy of innovation and a commitment to quality that continues to set the standard for compression solutions in the most demanding applications. From the harsh environments of oil and gas fields to the precise requirements of petrochemical plants, Cameron compressors are trusted to deliver consistent, dependable performance. This post explores the strengths of Cameron compression systems and how they empower critical operations across various sectors, highlighting the engineering excellence that underpins their renowned reliability.
A Legacy of Excellence
Cameron's history in the compression industry spans over a century, marked by continuous innovation and a dedication to providing robust, high-performance solutions. Their expertise in engineering and manufacturing has made them a trusted name in sectors such as oil and gas, petrochemicals, and industrial processing, where reliable compression is essential for operational success. Throughout their history, Cameron has consistently pushed the boundaries of compressor technology, developing innovative solutions that meet the evolving needs of their customers. This commitment to excellence is now further strengthened through their integration with Schlumberger's global network and technological resources.
Cameron Compression Systems: Engineered for Performance
Cameron offers a wide range of compression systems designed to meet the specific needs of diverse applications. Their product portfolio includes: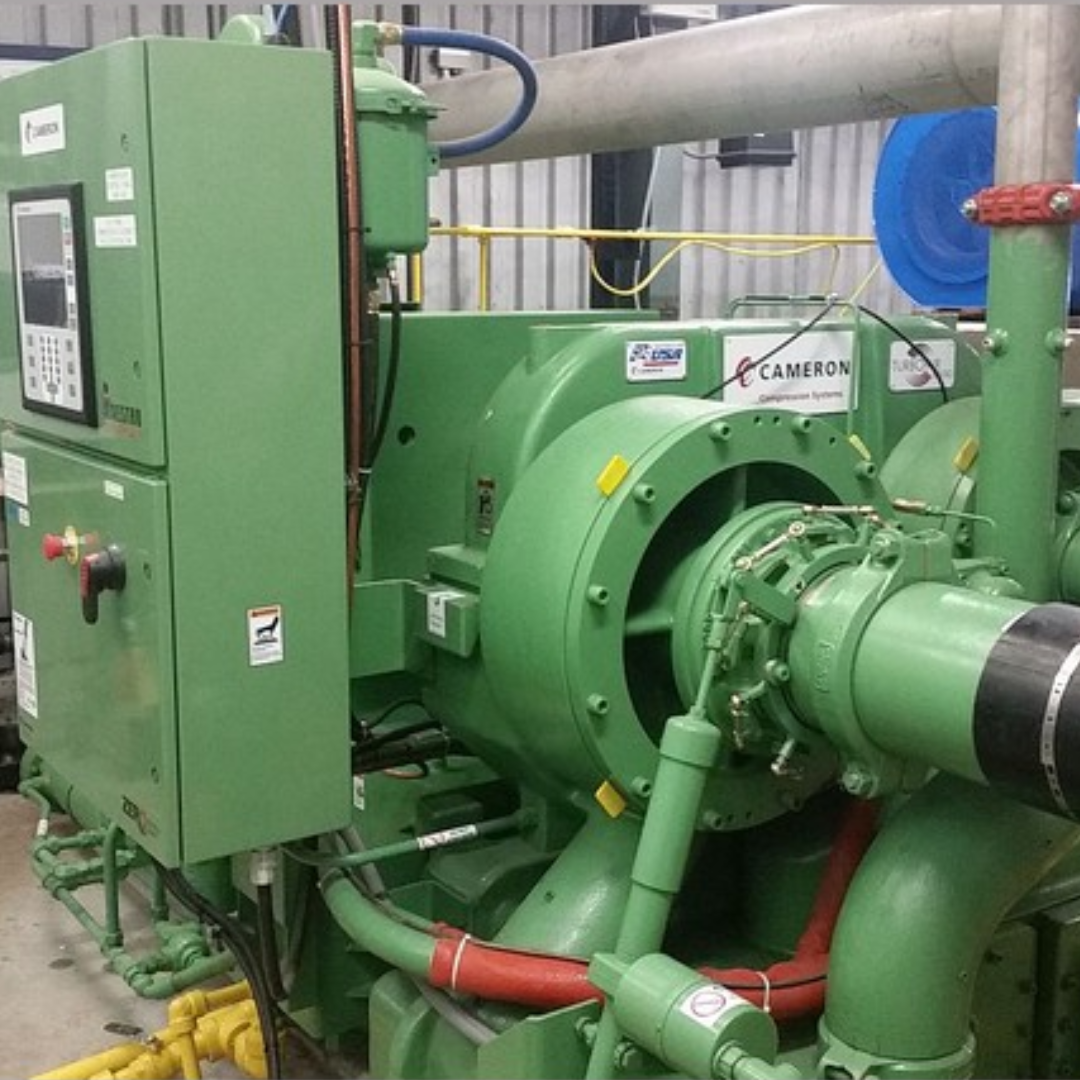
- Reciprocating Compressors: Cameron's reciprocating compressors are known for their high-pressure capabilities, robust design, and exceptional reliability. They are widely used in demanding applications such as:
-
Gas Gathering and Processing: Compressing natural gas from wellheads for transportation and processing.
-
Gas Lift: Injecting high-pressure gas into oil wells to enhance production.
-
Pipeline Compression: Boosting the pressure of natural gas in pipelines for long-distance transport.
-
Refinery Processes: Providing compressed air or gas for various refinery operations.They come in various configurations, including single-stage and multi-stage designs, to accommodate different pressure and flow requirements
- Centrifugal Compressors: These compressors excel in high-volume, low to medium-pressure applications. Cameron's centrifugal compressors are known for their:
- High Efficiency: Optimized aerodynamic designs and advanced materials minimize energy consumption.
- Reliability: Robust construction and precision engineering ensure long-term performance.
- Low Maintenance: Fewer moving parts compared to reciprocating compressors result in reduced maintenance requirements.
They are commonly used in applications like:
- Gas Processing: For chilling and liquefaction of natural gas.
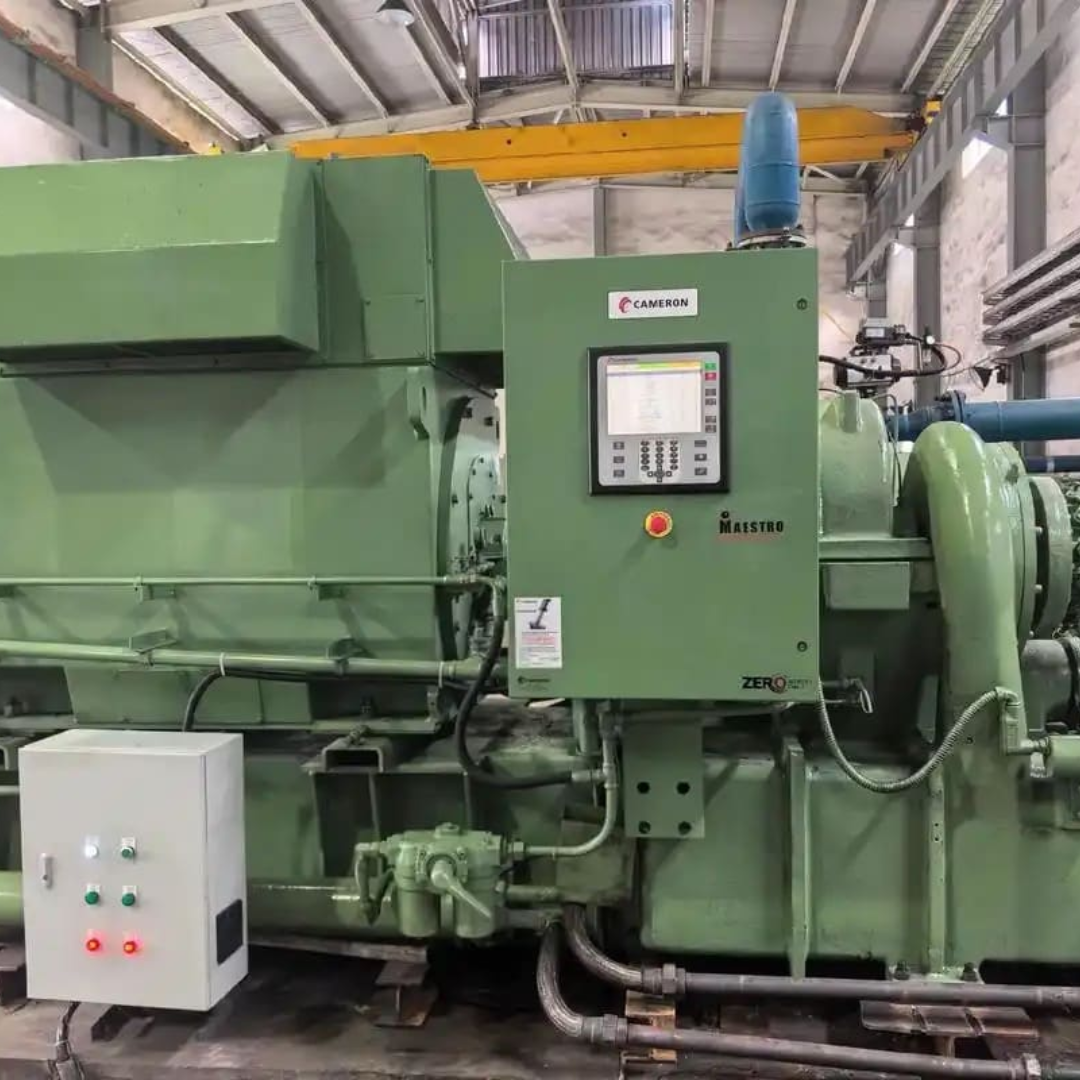
- Petrochemical Plants: Providing compressed air or gas for various processes.
- Industrial Refrigeration: Large-scale refrigeration systems.
- Screw Compressors: Cameron offers screw compressor packages for specific applications that require the unique advantages of this technology, such as in certain gas processing or industrial applications. They provide oil-free air in a compact design.
- Integrated Compression Systems: Cameron specializes in designing and manufacturing fully integrated compression packages, tailored to meet the unique requirements of each project. These packages often include not only the compressor but also:
- Drivers: Electric motors, gas engines, or gas turbines.
- Cooling Systems: Air-cooled or water-cooled heat exchangers.
- Control Systems: Advanced control panels and automation systems for precise operation and monitoring.
- Auxiliary Equipment: Scrubbers, separators, pulsation dampeners, and other components as needed.
- This integrated approach ensures seamless compatibility between components, simplifies installation, and optimizes overall system performance.
Key Features and Benefits
Cameron compression systems are distinguished by several key features: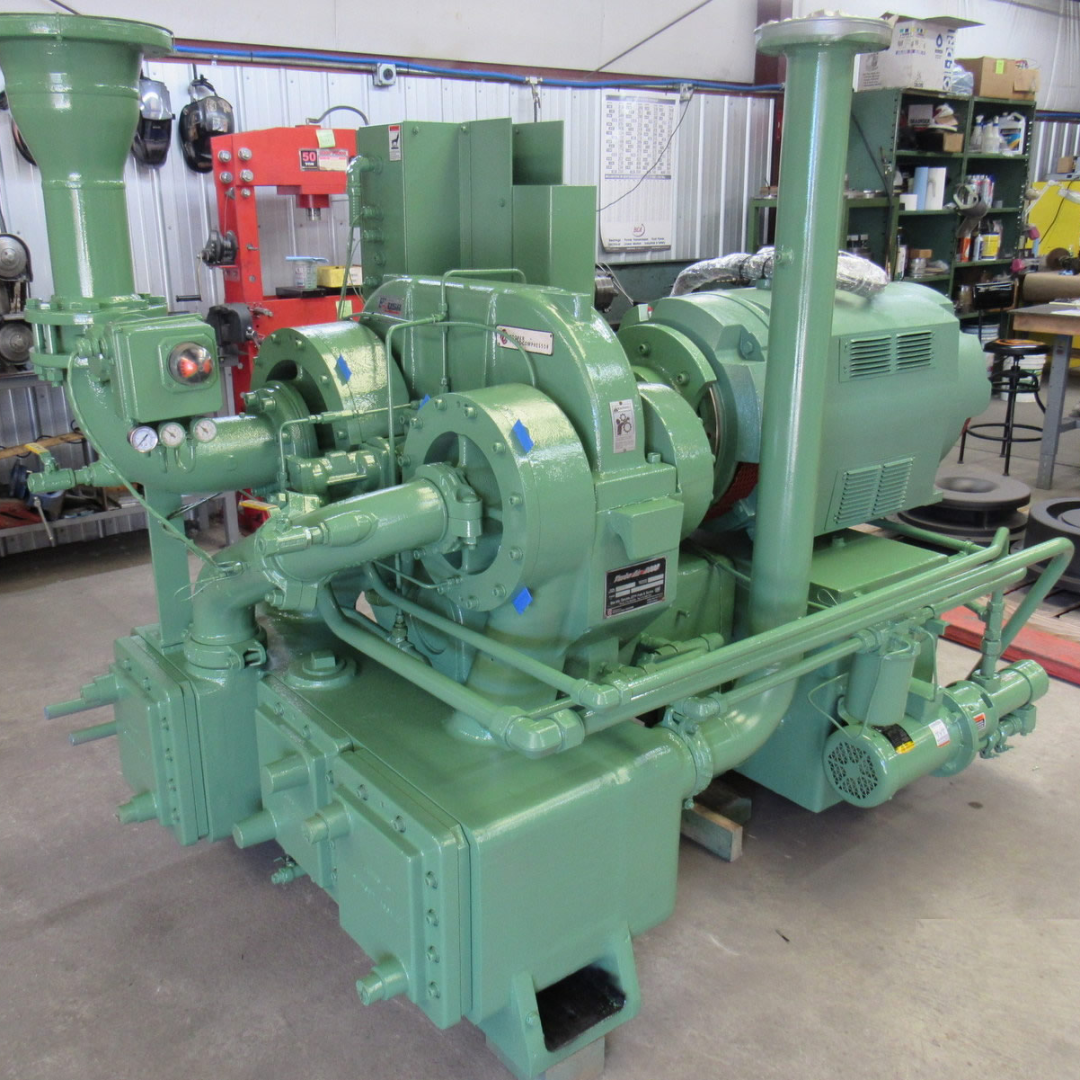
- Engineered Reliability: Cameron's rigorous engineering and manufacturing processes, including finite element analysis (FEA), computational fluid dynamics (CFD), and stringent quality control, ensure that their compressors are built to last, even in the harshest environments.
- Robust Design: Heavy-duty construction, high-quality materials (e.g., specialized alloys for corrosive environments), and advanced engineering principles contribute to the exceptional durability of Cameron compressors.
- Efficiency Optimization: Cameron compressors are designed for optimal efficiency, minimizing energy consumption and reducing operating costs through features like advanced aerodynamic designs, optimized valve systems, and efficient cooling systems.
- Customization: Cameron offers a high degree of customization, allowing customers to tailor compression systems to their specific needs and operating conditions. This includes selecting the optimal compressor type, driver, cooling system, and control system for the application.
- Global Support: With Schlumberger's global network of service centers and technical experts, Cameron provides comprehensive support throughout the lifecycle of their equipment, including installation, commissioning, maintenance, and repair.
Applications Across Industries
Cameron compression systems play a critical role in various industries:
- Oil and Gas: From wellhead compression to gas processing, pipeline transportation, and enhanced oil recovery, Cameron compressors are essential for efficient and reliable operations across the entire oil and gas value chain.
- Petrochemical: Cameron's robust designs and high-pressure capabilities make them ideal for demanding petrochemical applications, such as the production of plastics, fertilizers, and other chemical products.
- Industrial Processes: Cameron compressors are used in a variety of industrial processes, including refrigeration, air separation, power generation, and general manufacturing, where reliable compressed air or gas is required.
Blackhawk Equipment: Supporting Cameron Compression Systems
Blackhawk Equipment recognizes the value and performance that Cameron compression systems offer. As a trusted supplier, we are committed to providing our customers with access to these world-class compression solutions. Blackhawk can also service this equipment, and our team of experts can assist in selecting the right Cameron compressor for your specific application, ensuring optimal performance and long-term reliability. We understand the critical role that compression plays in your operations, and we are dedicated to providing the support you need to keep your systems running smoothly and efficiently.
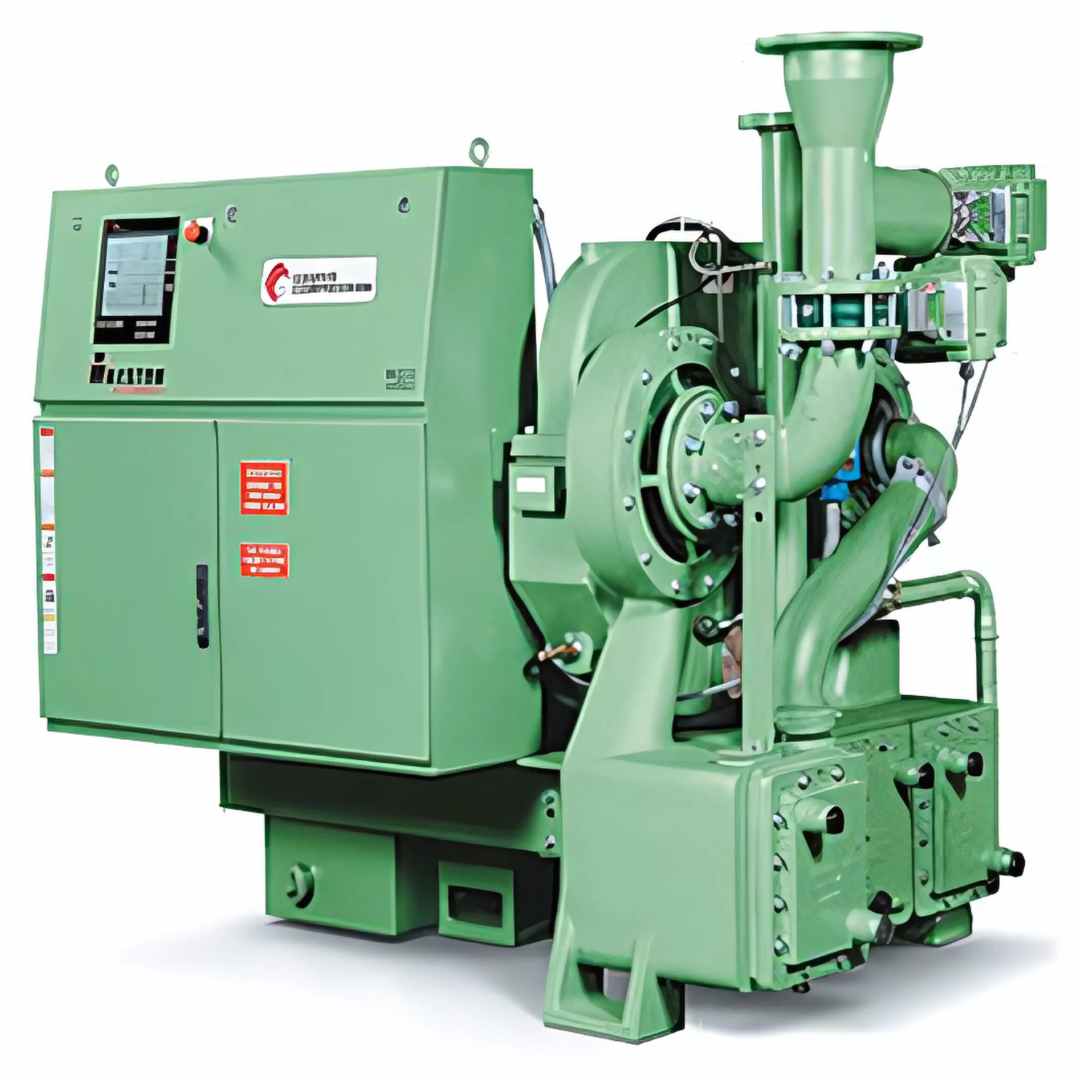
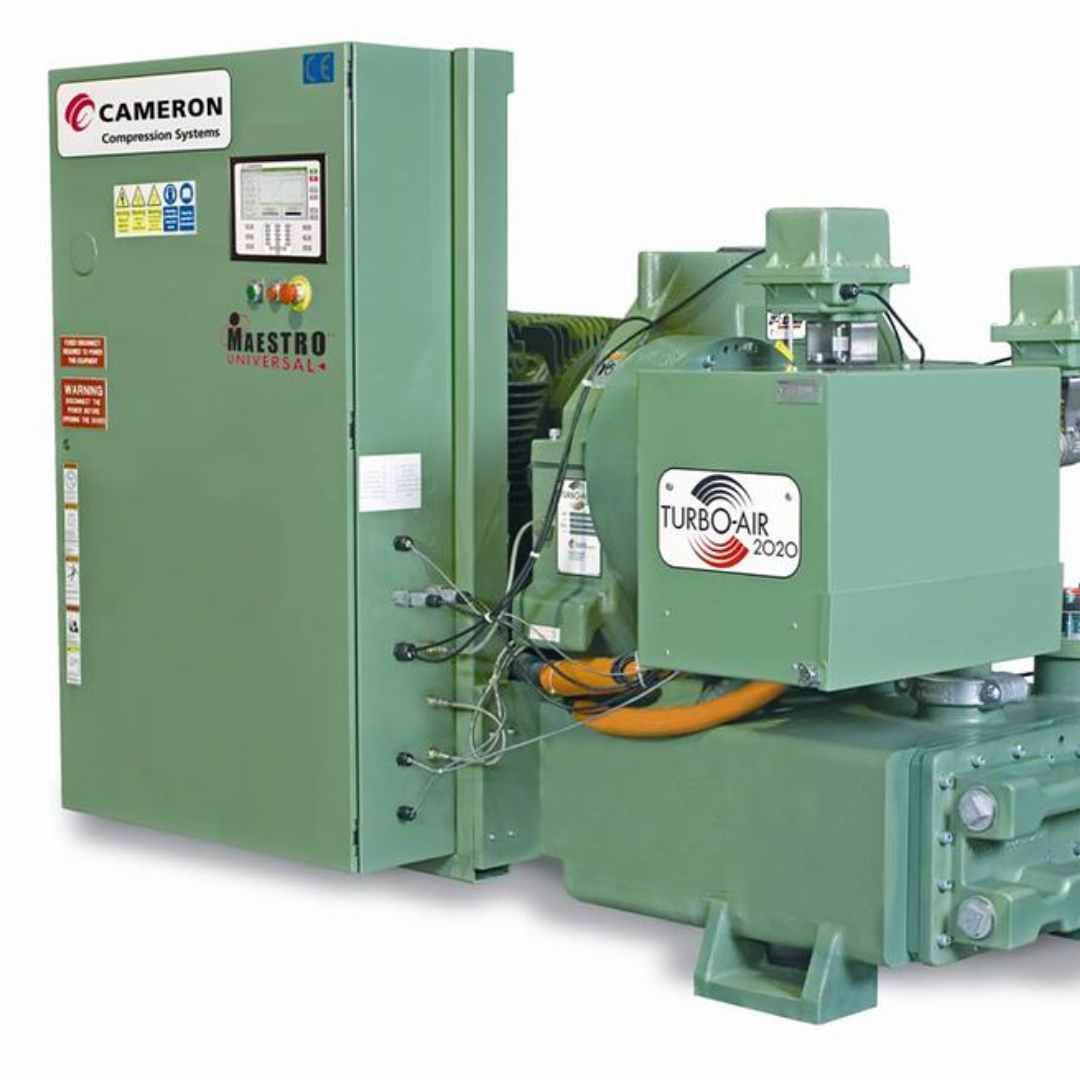

To sum up:
Cameron compression systems represent a legacy of engineering excellence, providing reliable and efficient performance in the most demanding applications. Their robust design, coupled with a commitment to innovation and customer support, makes them a preferred choice for industries where operational continuity is paramount.
The integration with Schlumberger further strengthens Cameron's capabilities, providing access to a global network of expertise and resources. Contact Blackhawk Equipment today to explore how Cameron compression solutions can enhance your operations and to learn more about the comprehensive support we offer for these exceptional systems. Our team is ready to help you find the perfect fit for your application, ensuring you have the reliable compression power you need to succeed.